河南金伟自动化设备有限公司
专业玻璃钢拉挤模具与设备制造商,为客户提供高品质自动化设备及解决方案
河南金伟自动化设备有限公司位于中国河南省安阳市滑县白道口镇,是一家专注于玻璃钢复合材料制造领域的技术企业。致力于为客户提供高品质的自动化设备及解决方案,主要产品包括玻璃钢拉挤模具、液压拉挤设备、伺服液压牵引机、导毡器、切毡机、树脂分散机等。20年经验,服务客户超3000家,多种规格可选,价格实惠,满足各种定制需求。核心优势:· 技术创新与研发能力:公司拥有一支经验丰富、技术高超的研发团队,不断探索新技术的应用,确保产品性能始终处于行业超前地位。· 产品质量与可靠性:我们从原材料采购到成品检验,每一步都经过严格的质量控制,确保设备稳定可靠。· 定制化解决方案:我们深入了解每一位客户的具体需求,提供从设计、制造到安装调试的一站式服务,确保客户得到更合适的解决方案。· 售后服务与支持:我们建立了覆盖全国的服务网络,提供24小时快速响应服务,确保客户设备的正常运行。
-
服务客户3000
+
家
-
产品体系50
+
种
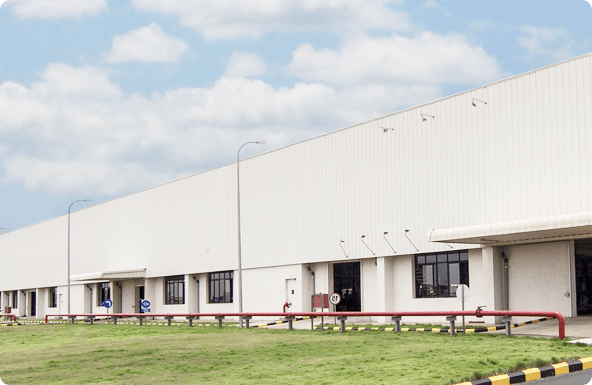
以优质的产品质量,服务于新老客户
为客户定制满意的产品,全天候、全时制、全方位提供服务
-
伺服液压设备润滑不足的隐性代价伺服液压设备作为工业自动化领域的核心动力单元,凭借高精度、快响应等特性,广泛应用于航空航天、新能源汽车制造等高要求场景。然而,2023年某第三方机构调研显示,国内23.6%的伺服液压设备故障与润滑管理不当直接相关。润滑系统看似基础,却直接影响设备寿命、能效与运动控制精度。伺服液压设备润滑需求的三大核心逻辑1. 降低动态摩擦损耗,保障控制精度伺服液压设备依赖电液伺服阀实现微米级运动控制,阀芯与阀套间隙通常仅3-5微米。若润滑油膜厚度不足(<1μm),金属直接接触将导致摩擦系数激增。实验表明,当油液黏度下降20%时,某型号伺服缸的重复定位误差扩大至±0.15mm,远超设计标准(±0.05mm)。2024年某锂电池极片轧机案例中,因未采用耐高温酯类润滑油,导致伺服阀在80℃工况下滞环特性恶化,整机良品率骤降12%。2. 维持密封系统动态稳定性伺服液压设备的密封件需在30MPa高压与高频交变载荷下工作。最新研究发现,润滑油在聚氨酯密封圈表面形成的边界润滑层,可降低60%的启动摩擦力。某德国品牌2023年推出的纳米石墨烯添加剂,能使密封件寿命延长至8000小时(较传统产品提升40%),特别适用于新能源车架焊接机器人等高频启停场景。3. 抑制油液污染链式反应伺服液压系统对油液清洁度要求达ISO 15/13/10级,1克污染物可产生超过500万个>5μm颗粒。润滑油通过吸附磨损碎屑、中和酸性物质,阻断“磨损-污染-加剧磨损”的恶性循环。2024年浙江某压铸企业加装循环润滑过滤模块后,伺服泵的累计故障间隔时间(MTBF)从1800小时提升至3200小时。伺服液压设备的润滑管理已从“基础维护”演变为“性能增强战略”。短期需优化油品选型(如匹配HLP68级液压油与0.1μm精密过滤器),长期则需构建智能润滑体系:通过嵌入式油质传感器实时监测黏度、水分及颗粒物浓度,结合数字孪生技术预测换油周期。在工业4.0背景下,润滑技术的突破将成为伺服液压设备突破扭矩密度极限(当前行业最高达2.1N·m/kg)、拓展应用场景的关键支撑。唯有将润滑纳入设备全生命周期管理,方能释放伺服液压系统的终极潜能。2025-04-21
-
伺服液压设备中的“伺服”解析:核心技术与应用革新在工业自动化与精密控制领域,伺服液压设备凭借其高精度、快速响应的特性,正成为高端制造业的关键装备。而“伺服”作为这类设备的核心技术,其定义与实现方式直接影响设备性能。近年来,随着智能算法与新材料的发展,伺服液压设备中的伺服系统已从传统机械控制升级为数字化闭环控制。1. 何谓“伺服”?——从概念到技术实现“伺服”(Servo)源自拉丁语“Servus”,意为“跟随”,其本质是通过实时反馈实现目标动作的精准复现。在伺服液压设备中,伺服系统由控制器、执行器(如伺服阀或伺服电机)、传感器三部分组成,形成“指令-反馈-修正”的闭环控制链。与传统液压设备相比,伺服液压设备的核心差异在于:动态响应能力:伺服阀响应时间可达毫秒级(如1-2ms),可精确匹配高频动作需求(如冲压机床的连续作业);能量效率提升:通过压力-流量复合控制,系统能耗降低30%-50%;精度控制:位置重复精度可达±0.01mm,适用于半导体封装、航空航天等高精度场景。2. 伺服技术在液压设备中的创新应用近年来,伺服液压设备的伺服系统呈现两大技术突破:智能化控制算法:融合PID(比例-积分-微分)与模糊控制算法,例如某厂商开发的“自适应伺服控制器”,可依据负载变化实时调整参数,避免传统系统因外部干扰导致的震荡问题;直驱式伺服液压技术(DDSH):取消传统液压泵站,采用伺服电机直接驱动液压缸,减少能量传递损耗,同时实现静音化(噪声<65dB),该技术已在新能源汽车电池模组生产线中广泛应用。此外,伺服液压设备通过物联网(IoT)技术实现远程监控与预测性维护。例如,某德国品牌的伺服液压注塑机内置振动传感器,可提前3周预警伺服阀磨损故障,减少停机损失。“伺服”不仅是伺服液压设备的技术标签,更是其突破传统液压瓶颈的核心驱动力。从闭环控制到智能化升级,伺服系统通过高精度反馈与动态调节,为工业设备赋予了“柔性”与“智能”的双重属性。未来,随着碳化硅功率器件、数字孪生技术的渗透,伺服液压设备将在节能性(能效比提升至90%以上)与多场景适应性(如深海机器人液压关节)上持续突破,成为智能制造时代不可或缺的“精密之手”。2025-04-16
-
伺服液压设备的智能化跃迁伺服液压设备作为现代工业动控领域的“精密心脏”,其系统组成直接决定设备响应速度与能效水平。据《2023全球液压技术白皮书》显示,伺服液压设备在新能源装备、航空航天等高端领域的渗透率已达42%,较传统液压系统节能35%以上。随着工业4.0推进,中国伺服液压设备市场规模预计2025年将突破180亿元,其核心组件正向数字化、高集成化迭代。1. 高动态伺服电机驱动单元作为动力源,永磁同步伺服电机采用矢量控制技术,转矩密度较传统电机提升60%。某德系品牌2023年推出的双绕组电机,可在0.5ms内实现±0.01%的转速精度调节,适配300Hz高频响液压泵。其内置振动抑制算法,使设备在注塑机合模阶段能耗降低18%。2. 智能液压泵阀集成模块多联式变量泵组通过CANopen总线与伺服控制器直连,压力-流量复合控制精度达0.1MPa/0.1L/min。如某国产设备集成数字式比例阀,采用纳米级阀芯镀层技术,泄漏量控制在0.05mL/min以内,满足半导体设备微米级定位需求。3. 分布式传感网络系统设备部署16通道磁致伸缩传感器阵列,实时采集油温(±0.1℃)、压力(±0.02%FS)、位移(0.5μm)等参数。某日企开发的薄膜压力传感器嵌入油缸活塞,可捕捉0.01ms级的压力波动,提前预判密封件失效风险。4. 边缘计算控制中枢基于ARM Cortex-A72架构的嵌入式控制器,运行实时Linux系统,支持EtherCAT千兆通讯。其内置数字孪生引擎可在线优化PID参数,某风电变桨系统应用案例显示,动态跟踪误差减少53%。5. 能效优化执行机构采用轻量化陶瓷活塞杆(重量减轻40%)与自适应蓄能器,通过压力能回收技术实现装机功率下降25%。某压铸机改造项目实测显示,伺服液压设备在保压阶段可回收85%的惯性能量。伺服液压设备正从单一动力单元向智能感知-决策-执行系统演进。核心组件的协同创新带来三大突破:①动态响应速度突破10kHz带宽限制;②系统能效比达93%(ISO 4409标准);③支持5G-TSN网络下的多设备同步控制。据中国液压气动密封件协会预测,2024年搭载AI能耗优化算法的设备将占新增市场的65%,而氢能压缩机用超高压伺服液压设备(≥100MPa)年需求增速超120%。建议设备厂商重点攻关高频响密封材料(如聚醚醚酮复合涂层)与故障预测性维护系统,以抓住新能源汽车一体压铸、人造太阳装置等新兴市场需求。
-
液压伺服设备:智能工业的核心动力伺服液压设备作为工业自动化领域的“精密神经”,通过闭环控制技术实现了力、速度、位置的毫米级动态调节。据Global Market Insights 2024年报告,全球伺服液压设备市场规模预计以8.5%的年均增速持续扩张,中国市场份额占比超35%。在智能制造与“双碳”战略驱动下,伺服液压设备正从传统工程机械向半导体封装、航空航天等高端领域渗透。1. 伺服液压设备的核心结构伺服液压设备由动力模块、控制模块与执行模块构成全闭环系统:动力模块:伺服电机驱动双向变量泵(如力士乐A4VSO系列),流量精度达±0.1L/min,能耗较传统液压系统降低40%以上(2023年伊顿液压实测数据)。控制模块:集成PID算法的高响应控制器(如博世Rexroth HNC100),采样频率达2kHz,可实时补偿负载波动与温度漂移。执行模块:采用低摩擦缸体(摩擦系数≤0.01)与高频响比例阀(响应时间<5ms),如派克PV Plus系列,确保定位精度±0.02mm。2. 伺服液压设备的分类演进2.1 按驱动方式划分电动伺服液压系统:搭载永磁同步电机(如西门子SIMOTICS S-1FK2),功率密度提升30%,适配精密注塑机与光学镜片加工。电液复合伺服系统:融合电动缸与液压缸优势(如2023年川崎重工K3V系列),在盾构机推进系统中实现推力2000kN±1%的精准控制。2.2 按应用场景划分重载高精度型:风电叶片疲劳测试机采用多级压力补偿技术,轴向加载力波动<0.5%。微型伺服液压单元:医疗机器人驱动模块重量<10kg,输出压力可达20MPa(费斯托2024年新品参数)。3. 伺服液压设备的技术突破能效跃升:智能变频技术使待机功耗降至50W以下(丹佛斯iC2-Micro系统),符合ISO 50001能效标准。数字孪生集成:通过AMESim仿真平台预演设备动态特性,调试周期缩短60%(2024年三一重工案例)。材料革新:碳纤维增强缸体(疲劳寿命延长3倍)与陶瓷涂层阀芯(耐温400℃)成为主流配置。伺服液压设备正通过结构轻量化、控制数字化与材料高端化,突破传统液压技术的性能边界。在新能源装备领域,其压力控制精度已突破0.1%FS(满量程),同时能耗较2019年平均下降52%。据《中国液压工业年鉴2024》预测,伺服液压设备在半导体封装设备的渗透率将于2027年达到68%。这一兼具高动态响应与绿色基因的技术体系,将持续赋能工业4.0时代的精密制造革命。
-
伺服液压设备与变频器的技术耦合趋势伺服液压设备凭借高精度、快速响应的特性,在工业机器人、精密机床等领域广泛应用。随着“双碳”目标推进与智能制造升级,传统液压系统的能耗与效率矛盾日益凸显。近年来,变频器作为电机驱动核心器件,通过与伺服液压设备的深度集成,正在重构液压动力系统的控制逻辑。1. 变频调速实现能耗动态优化传统定量泵液压系统存在“溢流损耗”,而伺服液压设备搭载变频器后,可通过调节异步电机转速精准控制液压泵输出流量。例如,伊顿公司2023年推出的EVP20系列伺服液压系统,集成三菱FR-F800变频器,使注塑机在保压阶段电机转速降至额定值30%,综合节能率达45%。这种“按需供能”模式,既契合伺服液压设备的高效需求,又满足ISO 50001能源管理体系要求。2. 提升动态响应与控制精度伺服液压设备对压力/流量闭环控制要求苛刻,变频器的矢量控制技术可将电机转速波动控制在±0.2%以内。德国博世力士乐开发的CytroPac液压站,采用丹佛斯VLT®变频器与数字液压阀协同控制,在汽车焊接机器人应用中实现0.01mm级位置重复定位精度。2023年国内企业研发的磁悬浮变频器,更将电机响应时间缩短至5ms,突破伺服液压设备高频换向的技术瓶颈。3. 智能变频器驱动系统升级新一代变频器内置AI算法与物联网模块,赋予伺服液压设备预测性维护能力。西门子G120X变频器通过采集液压系统压力、油温等数据,可提前72小时预警泵阀故障。在风电变桨系统中,ABB ACS880变频器与伺服液压执行机构联动,根据风速变化实时调整桨距角,单台风电机组年发电量提升8%。这类智能化改造,正在重塑伺服液压设备的运维生态。伺服液压设备与变频器的技术融合,标志着液压传动从“粗放供能”向“智能控能”的范式转变。随着SiC(碳化硅)功率器件、数字孪生技术的普及,2025年全球伺服液压系统变频器渗透率预计突破65%(据Grand View Research数据)。建议企业在设备改造中优先选用支持EtherCAT通信协议的变频器,并通过数字仿真优化参数匹配,充分释放伺服液压设备在精密制造、新能源等领域的应用潜力。
-
拉挤模具的科学保养与维护在复合材料连续成型工艺中,拉挤模具作为液压式玻璃钢拉挤设备的核心部件,其状态直接影响型材的尺寸精度、表面质量及生产效率。随着2023年全球制造业对绿色生产与降本增效需求的提升,拉挤模具的保养策略正从传统的“被动维修”转向“预防性维护”。日常清洁与表面防护:预防磨损与树脂残留拉挤模具的连续工作环境易导致树脂固化残留和纤维碎屑堆积。每日停机后需使用专用铜质刮刀清除模腔内的半固化树脂,避免高温碳化形成硬质结块(研究表明,残留物厚度超过0.1mm会使模具导热效率下降15%)。2023年,某企业引入激光清洗技术,通过脉冲激光精准去除模具死角污染物,较传统化学清洗效率提升40%。此外,模具表面应定期涂覆耐高温脱模蜡或聚四氟乙烯涂层,降低摩擦系数,延长使用寿命。温控系统校准与优化:保障成型稳定性现代拉挤模具多采用多段独立加热设计,其温度均匀性直接决定树脂固化质量。建议每周使用红外热像仪检测模具表面温度分布,偏差超过±3℃需立即排查加热棒或热电偶故障。2023年行业创新案例显示,加装AI温控算法的模具可将温度波动控制在±1℃内,同时减少15%的能耗。冬季生产时需特别注意模具预热时间,避免冷态启动造成的热应力裂纹。结构精度监测与修复:应对微变形与磨损长期高压环境下,拉挤模具易发生入口锥角磨损和模腔微变形。每季度需采用三维扫描技术对比模具原始CAD模型,当模腔尺寸偏差超过0.05mm时,需进行纳米复合材料的激光熔覆修复。某头部企业2023年实验数据表明,定期修复可使模具寿命延长至30万米拉挤长度以上。对于玻璃纤维增强模具,应避免使用金属工具直接敲击,防止脆性断裂。在智能制造与可持续发展背景下,拉挤模具的保养已发展成为涵盖清洁技术、智能监测、精准修复的系统工程。通过建立每日清洁流程、周期性温控校验和数字化磨损管理,企业可将模具故障率降低60%以上,同时提升15%-20%的良品率。未来,随着物联网传感器与数字孪生技术的深度应用,拉挤模具的维护将实现从“周期性检查”到“实时健康管理”的跨越,为复合材料行业创造更大价值。
-
173-3906-7777
-
130-8385-3711
-
微信公众号